Blog Post Week 1 + 2: The Start
And, they’re off! The first week of the Design+Build Salt Lake construction experience at the Field of Dreams in Kearns is now complete, and though we got off to a slow start, we’re really moving forward with the first duplex (units 1 and 2) ready to be clad with Hardie board sheathing.
8/23/2018 - Day 1
began with a prep talk of sorts from the general contractor, followed by a blower door test to assess whether or not we were achieving the air tightness necessary to maintain a sealed building envelope. Unfortunately, we were well above the Passive House standard of 120 cfm of air infiltration (1,000+ cfm at test start), but by the end of the day we had reduced the number down to 750 cfm and identified a major problem area that would be resolved before the next test. Everyone joined in the effort to make improvements by taping and spray-foaming holes and gaps at corners, window openings, joist bays and anywhere else that Jörg’s thermal gun detected issues.
Air Infiltration Rate
Excel Spreadsheet that allows the calculation of Air Changes per Hour based on the building's area and volume. IN this screen shot, we manually added our target value of 200 CFM, which results in an air change rate of 0.9 per hour - a value to which these buildings have been designed to.
Blower Door Test
During the very first test, the results were at 1044 CFM, which the team was able to reduce to 750 CFM in the second test. Target value needs to be better than 200 CFM though, to guarantee the building's performance with regard to the chosen systems.
Unit Area
1,134 SF
Unit Volume
13,383
Test Pressure
-50P
Target Value
0.6ACH50
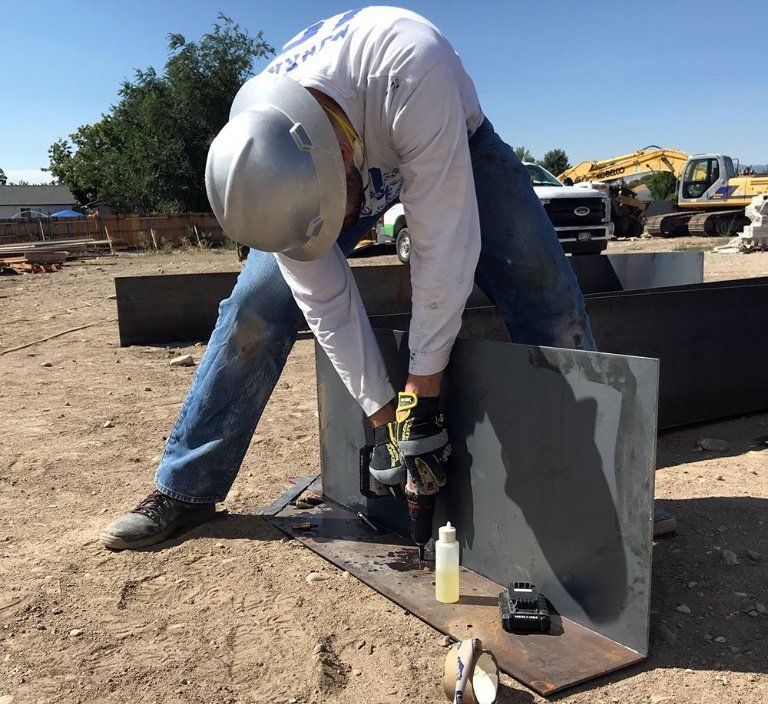
8/28/2018 - Day 2
provided new opportunities wherein students, individually and in small groups, took on a variety of tasks: sealing and patching the primary problem area discovered at the end of day 1; removing all the furring strips from the building’s exterior and hammering out the nails to prepare to attach the correct 2x4 strips; repairing the PEX radiant heat piping at unit 1; mounting the steel plate shades at the south, east and west upstairs windows; etc.
Only during the latter of these processes did we realize that the anchor holes for the side flanges weren’t close enough to the trimmer studs, and so Scot, and then later Joseph, had to tediously re-drill the holes. At least using the forklift to move people and steel posed an opportunity for Chris to reveal his expertise behind the controls.
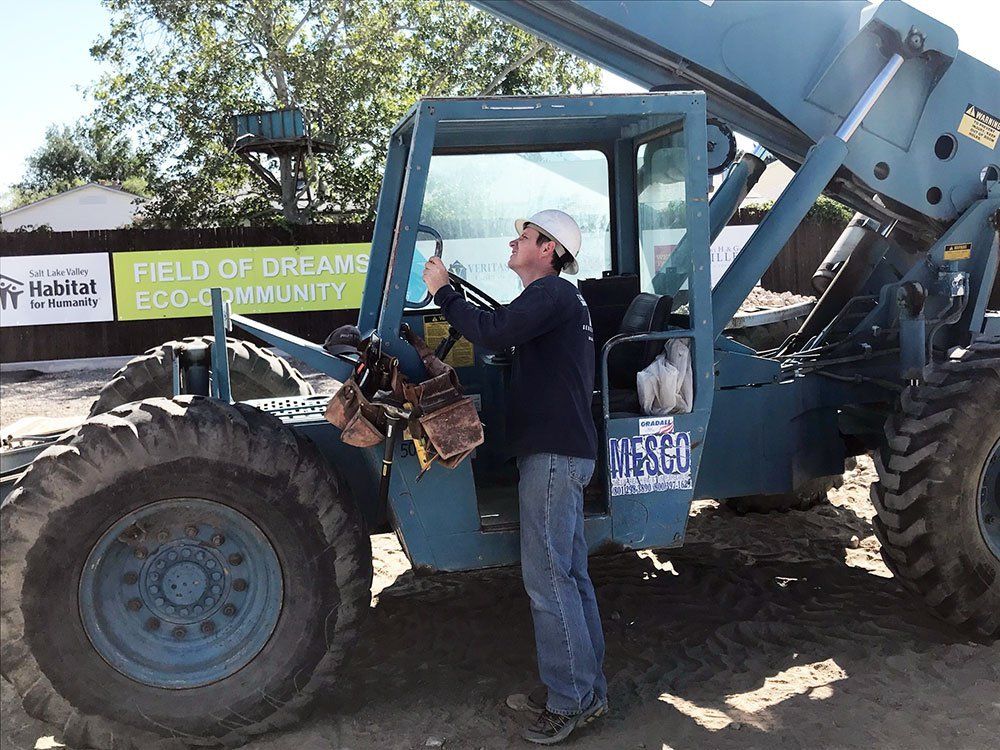
Titel hinzufügen
Schreiben Sie eine kurze Beschreibung.
Titel hinzufügen
Schreiben Sie eine kurze Beschreibung.
Titel hinzufügen
Schreiben Sie eine kurze Beschreibung.
Titel hinzufügen
Schreiben Sie eine kurze Beschreibung.
Mehr anzeigen
8/30/2018 - Day 3
Today's activities lifted spirits as most everyone got some kind of opportunity to use hammers, nail guns, staplers, saws, etc. for extended periods of time in what looked and felt like more constructive efforts. Several small crews worked on different sides of the units to attach new 2x4 furring strips (to prepare to receive cement panel board siding) as well as sheathe and house-wrap any remaining nooks or crannies. This time, Mitch got to show his prowess in operating the forklift, while Chris again schooled everyone with hammer, nail gun and (the appropriately-named in his case) skill saw. During a lunch time meeting with Jörg, each of three student groups discussed ideas and concepts surrounding a space-saving side project to be implemented in future housing units on the project. Mitch, Andy and Joseph discussed possibilities for a captain’s bed with drawers or shelves built into it; Chris, Dan and Scot looked at the constraints of a built-in, fold-out ironing board; and David, Scot and Zach weighed the challenges of constructing a stair with built-in storage compartments.
With week 1 under our belts, things are looking up as we watch the first duplex getting ready to receive its final skin and as we (hopefully) rev up for the start of concrete flatwork on the next two units. In spite of a soft start, each student looks to be settling in for more productive days and rewarding learning opportunities ahead.
- Scot Clark and Danile Guthrie